By Julia Purdy and Polly Lynn Mikula
RUTLAND—Friday, April 20, the Mountain Times staff made a field trip to Casella Recycling in Center Rutland, the heart of the Casella trash collection and recycling empire. The visit was made partly to resolve disagreements in the Mountain Times lunchroom and partly as an editorial decision to feature Rutland County’s recycling program as the statewide push to recycle intensifies.
The visit began with a brown-bag lunch in a small meeting room with Marc Okrant and Ashley Somers, both of the marketing team.
Okrant answered questions and gave an insider’s view of today’s recycling challenges. The mix of recyclable materials has changed considerably, he explained, especially since mail-order from Amazon and others has boomed. The value of commodities is also always in flux and it’s affected by international trade, tariffs and regulations. “China recently decreased its tolerance for the allowable contaminants in paper,” Okrant explained. This made it nearly impossible for Casella to compete reselling paper for a profit.
At the Zero Sort recycling center, the Mountain Times staff was led on a tour to see how various materials are sorted and bundled for resale to markets. The recyclables then become raw material for new product.
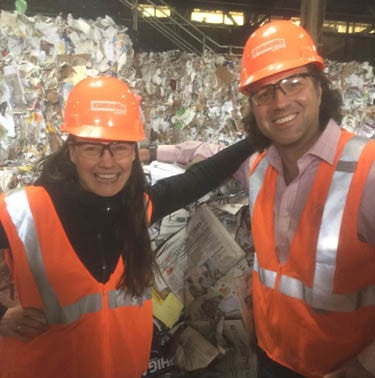
Polly and Jason Mikula, co-publishers, pose with a recycled copy of the Mountain Times.
General Manager Joe Soulia lead the tour of the Rutland facility. He explained that the plant handles approximately 36,000 tons per year of all materials in single-stream, also known as Zero-Sort, Casella’s trademark. Soulia compared the current volume to 500 tons, handled manually before Zero-Sort was introduced in 2012. Recycled material comes from a collection area that extends from Potsdam to Albany, N.Y. on the east; Manchester to north of Lebanon, N.H. on the west; across Vermont from about Montpelier to Vergennes to the north; and nearly to the Vermont border to the south. He said the plant could process another 30,000 tons by putting on a second shift.
The mountains of mixed materials that are trucked into the plant go through a mechanical and manual sorting process. About two dozen employees (“pickers”) stand at conveyor belts throughout the plant, grabbing items that should not be on that particular belt.
The first stage of sorting turns up all kinds of oddities: animal carcasses, live rats, car parts, even, once, a 10-foot boat! Lost valuables are also common: cash, diamond rings, important correspondence. Wallets are returned if they contain ID, Soulia said. Otherwise, it’s “finders keepers.” The day before, on April 19, the workers guessed they’d collected $500 cash collectively – all accidentally coming through on the belts.
At the end of the process, bales, sorted and graded for quality, are stacked ready for shipping. Tin cans are separated from aluminum by being floated over a magnet (it causes them to literally jump off the belts, see video clip at mountaintimes.info); they are then crushed into cubes that resemble modern art pieces. Each bale holds approximately 18,500 cans and is worth well over $1,000.
Recycling technology is constantly evolving, Soulia said. In the near future, Casella will invest millions of dollars into equipment that will turn out cleaner newspaper, and a special screen that will remove plastics from paper and separate the paper into its component elements to make picking easier.
Casella has eight recycling facilities throughout New England; Boston is the company’s largest recycling facility east of the Mississippi.
Like Okrant, Soulia commented that recycling is getting harder to do because of changes in markets and regulations on quality. But the reasons not to send materials to the landfill are “both economic and ethical,” he said.
In other words, in addition to helping the planet, recycling has its own bottom line: cost of processing has to pay for itself and turn a profit on at least some of the materials, and it does.
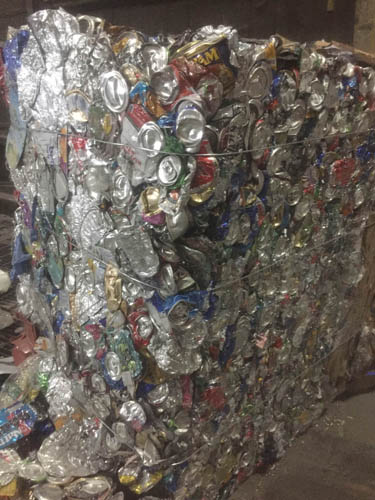
18,500 aluminum cans make up a bale.
His advice for recycling both at home and at work is to keep it simple: plastics, metals, paper (even greasy pizza boxes as long as there’s no cheese left in them), can get to markets easily as they’re all made up of single components.
Think about whatever might be attached to packaging, he said. “Wine bottles are complex,” he explained due to the metal casing on the neck of the bottle for decoration; this renders them non-recyclable. Plastic bubbles on a cardboard backing – such as is used with many toys, pens or batteries – must also be separated in order to be processed.
Supermarket bags can be recycled by bringing them back to the supermarket, but cannot be sorted out for recycling at the Zero Sort facility and instead end up in the trash.
As consumers, he cautioned that the triangular recycle stamps are often meaningless or misleading. Just because packaging may have them doesn’t mean it can actually be recycled practically, he said. Prepackaged fresh produce in a bag, for example, can’t be recycled because there is no way to sort it out from the rest. Buy veggies in a plastic carton, instead, he suggested.
Keep caps on plastic bottles, he added as a tip. Small objects (like lids) can slip through the screens and end up in the trash even if they are made of good plastics. Keeping the caps on bottles “at least gives them a chance to make it through,” he said.
“We are in charge as consumers,” he said.
Casella offers tours of its Zero Sort recycling center regularly – upwards of 27 times per year, Soulia guessed. School groups, businesses, clubs, camps, and individuals have witnessed the sorting-bundling operations at the facility at 1 Smith Road, in Rutland. For more information visit casella.com. For a virtual tour and further explanation of the sequential process at Rutland’s Zero Sort facility watch this three-minute video: youtube.com/watch?v=S_U6UuFLEGQ.
Photo by Joe Soulia
The Mountain Times team, pictured (l-r): Julia Purdy, Siobhan Chase, Ray Domingus, Jason Mikula, Polly Mikula, Lindsey Rogers, Erica Harrington and Curtis Harrington.